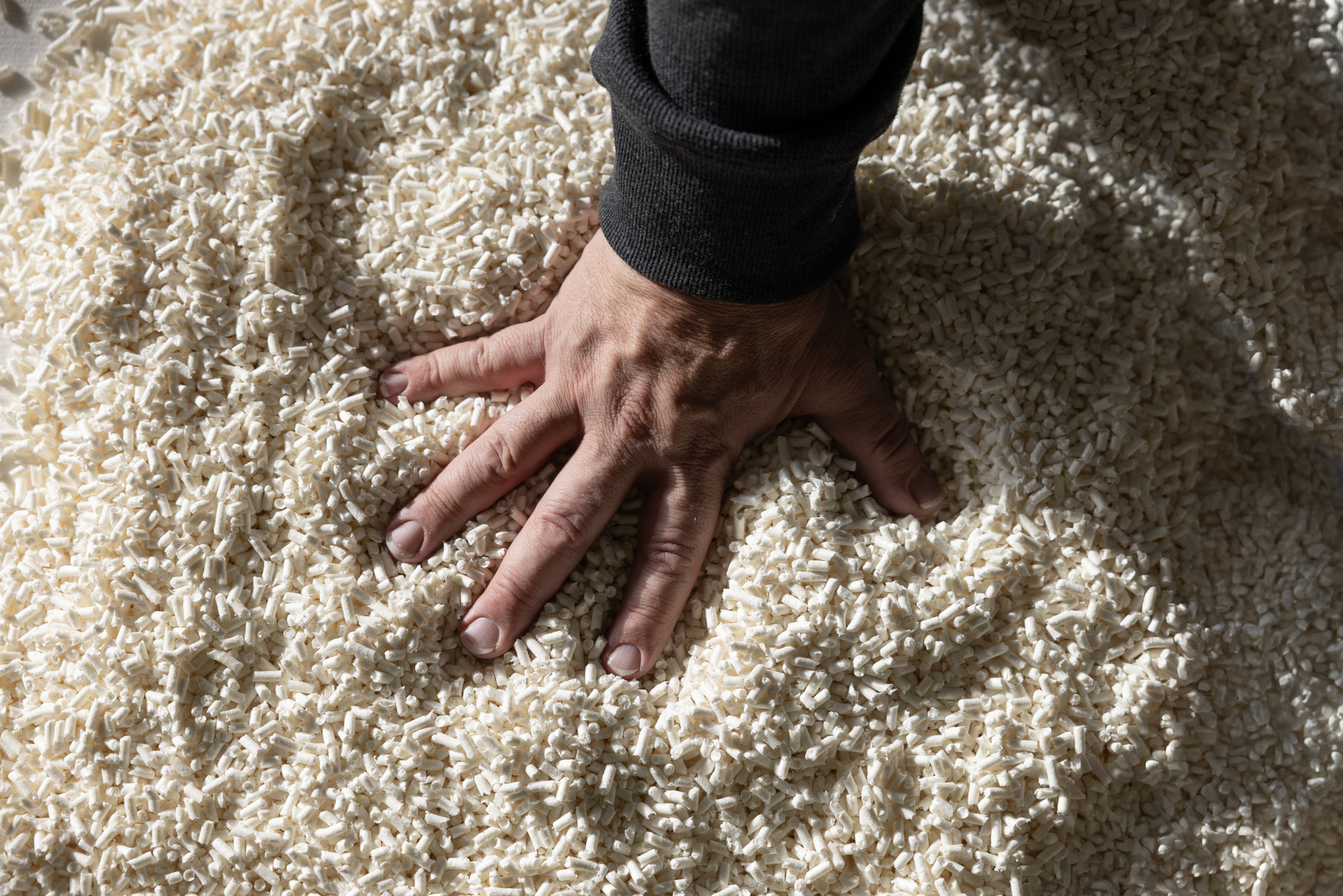
Syklocomp Biocomposite is a New, Eco-Friendly Alternative for Reinforcing Plastics
Made from recycled fibre and plastic, Syklocomp biocomposite provides a long-lasting, durable, and environmentally friendly alternative to glass fibre composites and other conventional reinforced plastics. Due to its technical properties, Syklocomp stands out as a leading commercial biocomposite with a significantly lower carbon footprint compared to traditional plastics.
In high demand for use in challenging technical applications
Until now, plastics used in technical applications have typically been reinforced with glass fibres or mineral fillers. Syklo is now introducing a new bio-based reinforcement that can replace these traditional reinforcement methods.
“Syklo’s technology combines mass production methods from both the paper and plastics industries; specifically, the wet-web process for composites and the proprietary DEVO extrusion technology we have developed. Our patented wet process protects the fibres and thus improves their reinforcing properties,” says Markku Nikkilä, Head of Business at Syklo.
The material is in high demand across a wide range of industries – not only for its excellent mechanical properties, but also for its ability to reduce environmental impact.
“The carbon footprint of Syklo’s biocomposite is significantly lower than that of traditional plastics. Syklocomp is a carbon-binding material, particularly well-suited for products with a long life cycle, such as those used in the car and electronics industries.”
A material of the future for the plastics industry
Eero Martikainen, Head of Partnerships at Syklo, shares that recycled and carbon-reducing sustainable material solutions are currently a major topic of discussion especially in the European plastics market due to legislative regulations promoting the circular economy.
“Through Europe, the EU is playing a leading role in steering the global plastics market towards a circular economy. With the introduction of new legislative targets, the use of recycled plastics is set to increase significantly, and there is growing market interest in solutions that reduce the carbon footprint of materials,” states Martikainen.
As Syklocomp is partly made from renewable raw materials, its carbon footprint is significantly lower compared to traditional plastics. The product is also highly recyclable, especially when compared to plastics reinforced with glass fibre, for example.
“It is fair to say that this is a material that meets the demands of our time. By using Syklocomp, you can not only reduce energy consumption during production and accelerate the production process, but also lower the carbon footprint of the product. These are all desirable features
from the perspectives of both production efficiency and environmental sustainability,” says Nikkilä.
Global solutions for more environmentally friendly practices
Syklo’s commitment to developing sustainable materials will be further reinforced with the completion of the plastics recycling plant and the state-of-the-art biocomposite plant at the Hyvinkää circular economy hub in early 2026.
“Although a lot of plastic ends up in the waste stream, it is also one of the best raw materials for recycling. With Syklo’s new technology, we can now recover plastic that was previously classified as waste for use in biocomposite production. Through our circular economy solutions, we aim to make global operating practices more sustainable,” says Markku Nikkilä.
4 facts: benefits of biocomposite
- Utilising biocomposite accelerates final product production and reduces energy consumption.
- Reduces the carbon footprint of long-lasting plastic products, as bio-based materials bind carbon throughout product life cycles.
- Biocomposite-reinforced plastic has a lower carbon footprint compared to, for example, plastics reinforced with glass fibre.
- Using biocomposite supports sustainable development and provides innovative solutions for a wide range of industrial applications.